ADVANCED TECHNOLOGY STRUCTURAL INDUSTRIAL CERAMIC PARTS
Mitalon supports you for the design process with its 20 years of research and development, Design and Production experience to mass production on parts and equipment produced from advanced technology industrial ceramic materials.
Technical Ceramics; they are high strength ceramic materials with hardness, toughness, wear resistance, thermal conductivity and thermal properties. It is produced from raw material with grain size below 0.1 mm.
According to the Place of Use and Features, we provide engineering and production support for the Types Below,
1. HIGH PERFORMANCE STRUCTURAL CERAMICS
-
- High strength
- High abrasion resistance
- Functional ceramics with high mechanical strength that are exposed to bending and compression loads.
They are used in many fields such as High performance structural ceramics, aviation, defense, textile, energy and automotive
2.STRUCTURAL CERAMICS USED IN ELECTRICAL, CUTTING AND MEDICAL FIELDS
- Electric Ceramics; areas with high insulation and mechanical strength
- Cutting Ceramics are used in lathe, drilling equipment, drilling, special cutting operations and excavation machines.
- Medical Ceramics; It is used in medical applications in the human body and It has areas of use such as bone implants, dental or other hard tissue implants, hip prosthesis
We design parts / equipment demands used in these areas, we complete material analysis, 2D and 3D dimensional modeling, and produce sample parts by passing to the prototype-manufacturing phase, by making the necessary tests and verification on the produced samples, we produce ceramic parts in accordance with the required mechanical and structural properties and go to the mass production phase.
MITALON STRUCTURAL INDUSTRIAL CERAMIC PRODUCTION PROCESS
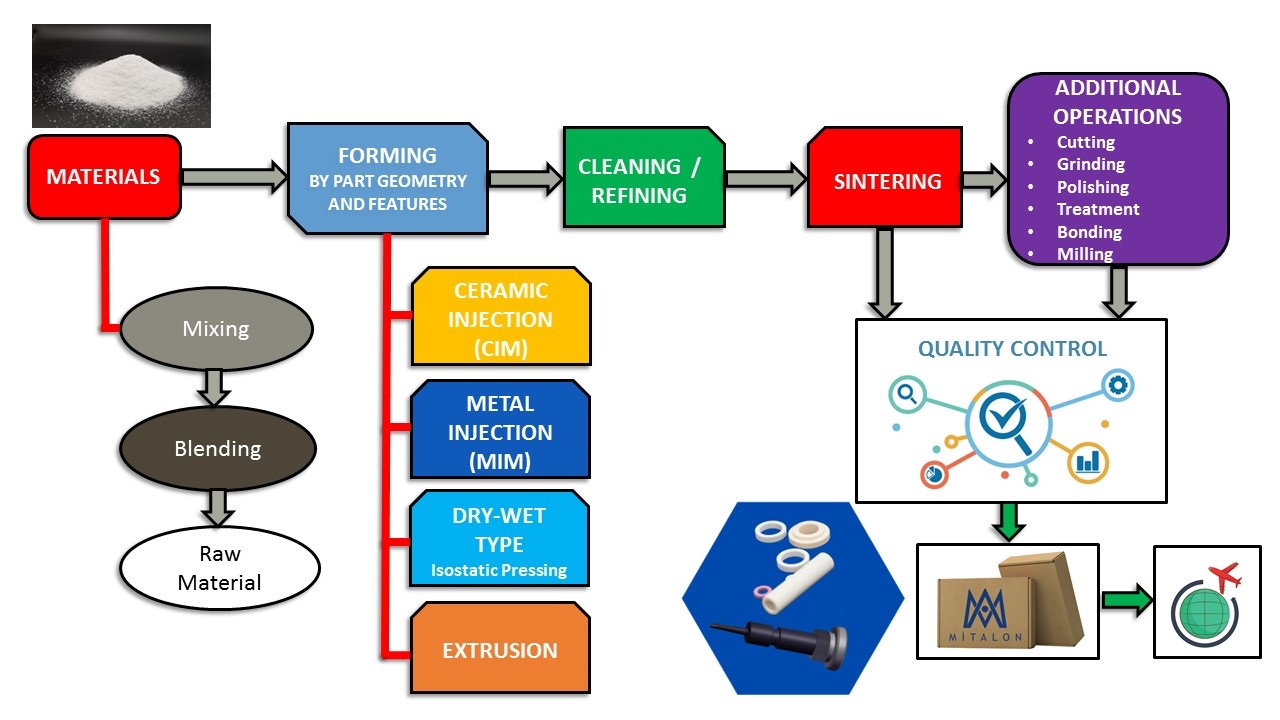
PRODUCTION METHODS
CERAMIC INJECTION MOLDING (CIM)
By using the Ceramic Injection Molding (CIM) method, which is an advanced production technology, together with our design and manufacturing expertise, we develop our high-tech structural ceramic parts; we support from design to mass production manufacturing.
With this production method, we offer cost-effective solutions for low and high volume orders of complex shaped technical ceramic parts.
By using our strong engineering infrastructure, we reduce the costs of ceramic parts with complex geometry by optimizing their operation and labor costs without compromising their functionality and quality.
We support our customers in selecting, designing and processing your advanced technology ceramic solutions with our material knowledge and expertise, together with the ceramic injection molding method.
We are here to help you gain maximum benefit from all the high-level features provided by Advanced Technology Ceramics at minimum cost.
ADVANTAGES OF MANUFACTURING WITH CERAMIC INJECTION MOLDING
- It enables the production of parts with complex geometry.
- Low Production Cost
- Improving product performance and increasing efficiency
- High volume productions
- Minimum variation in part geometry
- Fine surface quality
- Narrow tolerances (critical dimension requirements)
APPLICATIONS
The Ceramic Injection Molding method makes it possible to produce especially complex and complex geometry parts with minimum cost.
With this method, the manufacturing of high-strength structural ceramic parts for use in medical, automotive, aerospace and defense, textile, energy and similar sectors is made without sacrificing quality.
CERAMIC INJECTION MOULDING PROCESS(CIM)
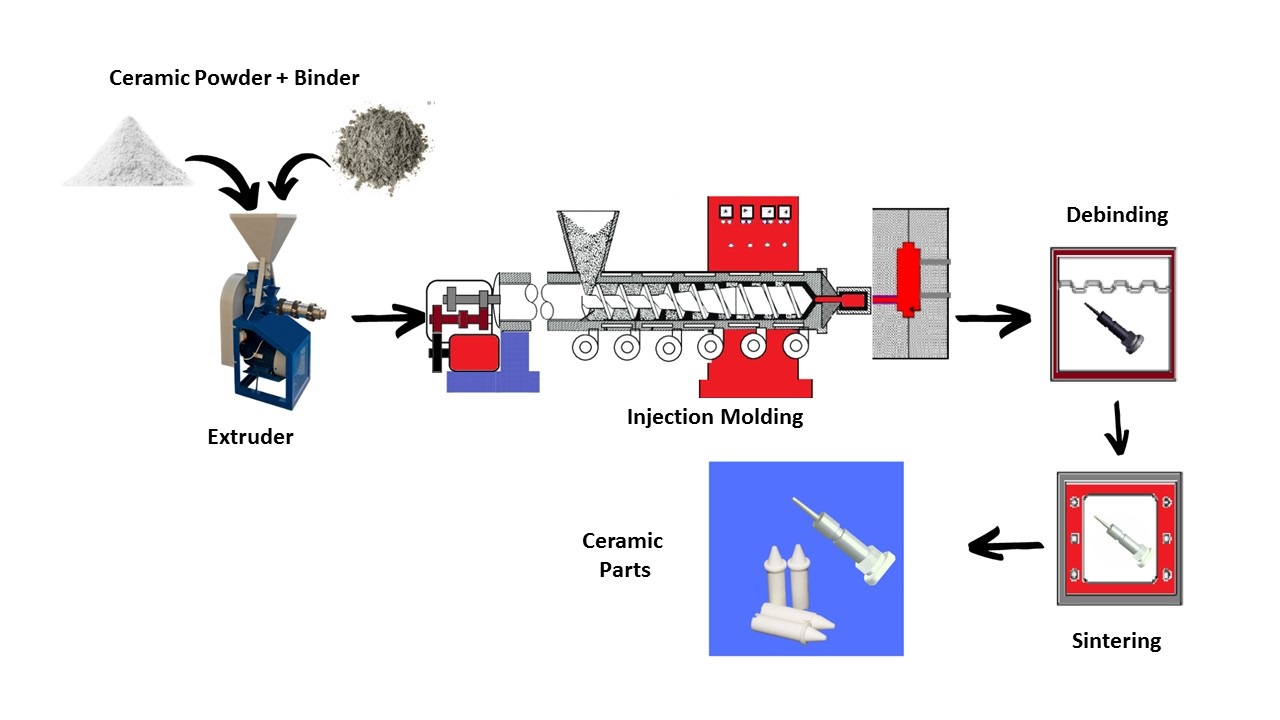
Production of ceramic materials by injection molding method consists of the following steps:
- With ceramic powder, suitable binders and additives are added and the mixture suitable for injection is obtained in a mixer.
- The mixture is transferred to injection and placed in the mold with the shape of the desired part with a pneumatic force applied by the rotation of a screw.
- The part is removed from the mold and removed thermally or chemically from the binder part in an oven.
- After the purification process, sintering process is started. At this stage, the heat and ceramic particles come together and become a solid part. At this stage, a dense ceramic component is obtained and the ceramic part gains mechanical and structural properties.
Additional operations such as polishing, sandblasting and cnc machining can be carried out on the parts upon customer request